The time-honoured bicycle drive system of pedal cranks, chain drive, and hub or derailleur gears has been in vogue for more than a century, and shows no sign of going away in the immediate future. But new thinking is starting to make an impact, and I am indebted to engineer Frank Moeller for his thoughts on the future of bicycle transmissions.
Inspiration
Frank’s inspiration came initially from a desire to produce a more efficient electric-assist bicycle. Electric bicycle motors can be more than 80% efficient, but a bicycle is a demanding environment, and motors generally work efficiently over a limited speed range.To keep the motor spinning close to this ideal speed, it needs to be near the pedals, as on the Panasonic drive system fitted to the Giant Twist.
This arrangement ties the motor speed to a comfortable pedal cadence, cleverly utilising the human engine to select a comfortable gear for both leg muscles and electric motor. Generally this works well, but the motor speed still varies a good deal, and with transmission losses, overall efficiency probably doesn’t exceed 60% in most cases. In other words, a typical power-assisted bicycle carries around a heavy, expensive battery, yet turns 40% of its capacity into worthless heat.That’s a better performance than most internal combustion engines, but on a bicycle – where weight is a serious issue – this poor performance is inexcusable.
Most electric vehicles throw power away on descents too.The motor could run as a generator, putting power back into the battery, but with most older designs, the noise and friction involved generally outweigh the potential benefit of recycling a little of the energy. How can matters be improved? it seems a number of avenues are worth exploring.
New Technology
Without going into too much technical detail, large ‘switched reluctance’ and ‘induction’ motors are already available, and they’re much more efficient than older types. Combine the best of these designs and there’s no reason why a new smaller ‘hybrid’ couldn’t be produced – light enough and efficient enough to fit inside a conventional bicycle hub, turning quietly and with little friction whenever the wheel turns. Such a motor would give assistance up hill and braking down hill. None of these new motor designs have yet been optimised for light electric vehicles, but engineers are working on the problems.
Today, motors and gears are usually so crude and noisy that the system necessarily spends much of it time disconnected.The new hybrid motor would be fitted inside the front hub, driven at speeds of 3,000rpm or more through a single-stage stepped epicyclic ear.This permanently engaged motor would run reasonably efficiently across a broad speed range and provide both assistance and braking.
It’s a neat idea, but Frank Moeller’s key conceptual breakthrough is to take this arrangement a step further and design a completely new bicycle drive system, based broadly on the transmission of the ‘hybrid’ petrol/electric Toyota Prius, but in this case combining and regulating human and electric power inputs.
Toyota Prius
The Prius has won many awards since its launch in 1997, and it’s easy to see why.This outwardly conventional car draws power from a small and relatively efficient petrol motor linked to the planetary gears of an epicyclic gearbox.
This is the same compact, efficient device used in hub gears, but in this case its purpose is to split the motor torque into two streams; one leaving through the sun gear to turn an electrical generator, and the rest going via the outer ring gear to the car’s wheels. On some designs the shaft to the wheels can pick up extra torque from an electric motor, but on others the motor is mounted at the other end of the vehicle to give four-wheel-drive.
This ‘Hybrid Synergy Drive’ might sound complicated, but it does away with the conventional clutch and gearbox, and performs most of the braking functions, because the clever ‘torque splitting’ arrangement functions as a continuously variable transmission. At low speed the petrol engine is turned off, and power is drawn from the batteries, via the electric motor. As the vehicle accelerates, the petrol engine is started, feeding power to the epicyclic. At first, the output shaft and wheels are turning slowly, so most of the power is diverted via the generator and converted to electrical power to feed the motor. This might be described as ‘first gear’. As speed rises, the ‘braking’ effect of the generator is progressively increased by electronic means, transferring more and more of the available torque directly to the wheels, with a smaller percentage being turned into electrical power by the generator. Above a certain road speed, the generator is given a high electrical resistance and the unit is effectively in ‘top gear’ As driver input and road conditions vary, the amount of power flowing from the generator to the motor is continuously adjusted, keeping the petrol engine turning at an optimum speed under almost all conditions.
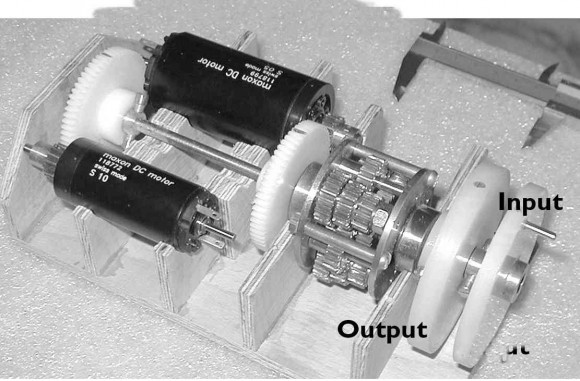
Bench test rig In both cases, input power is spilt into mechanical and electrical components, which are recombined in the output stage
For hard acceleration, extra power is supplied from the batteries, which will be recharged from the motor/generator when the going gets a little easier, or under braking. Back in low-speed stop-start urban driving conditions, the inefficient petrol engine is turned off, and the battery/electric motor combination takes over again. The torque split allows this clever transmission to make the best use of the very different characteristics of the electric motor and petrol engine, and it can be arranged to do the same with an electric motor and human ‘engine’. Ignoring the on-board battery for he time being, rider effort would be applied to the pedals as normal, and conveyed to the rear hub via a chain drive.
…the hub actually contains fewer parts than a typical five-speed hub…
In the hub, some of the human input would proceed direct to the wheel, with a proportion being diverted via a generator/motor electrical circuit, as on the Prius, but in this case the low pedal speed is geared up to give a high generator speed.When climbing a hill, the wheel would begin to slow, causing an increasing amount of torque to run via the generator.The electrical output from the generator would run just a few centimetres to an electric motor/generator, with the mechanical output being fed to the hub shell through a second epicyclic gearbox.
It might look complicated, but the hub actually contains fewer parts (and far fewer wearing parts) than a typical five-speed hub, and it’s fully automatic. And of course the system really lends itself to electric-assist, requiring just a battery and a few control circuits to turn the human-powered vehicle into a hybrid. As on the Prius, the battery would provide additional power for acceleration and hill-climbing, and absorb ‘waste’ power when coasting downhill. It would also be possible to recharge the batteries with pedal effort under favourable conditions.The major difference is that in stop-start town traffic, where the Prius petrol motor would be turned off, the primary input would be from the human ‘engine’ rather than the battery.
A New Era
A ‘torque split’ transmission would provide an HPV or assisted-HPV with a number of hitherto unattainable attributes. For the human ‘motor’, the hub gives a foolproof continuously variable transmission, with no gears to worry about.The hub could be set to provide either a constant input torque, constant pedal cadence, or a combination of the two, maintaining this optimum level under all conditions.The rider would simply point the bike in the right direction and start turning the pedals.Without the shock-loads imposed by frequent gear changes, maintenance would be reduced, and it might be possible to reduce the size and weight of components such as the crank and chain. And with the output motor able to function as a generator, recycling some of the power normally turned to heat by the brakes, the bicycle could be fitted with a small battery, or even a ‘super capacitor’ to store braking energy.This reduces the need for powerful brakes, reducing the size and weight of the braking system too.
Although bristling with technology, the hub would be simple, and easily fitted to a conventional bicycle.The one unit would replace the conventional gears, and reduce the weight and complexity of the transmission and brakes. On an electric bike, it would also replace the electric motor, wiring and control equipment.
Fact or Fantasy?
How close is this vision to fruition? In motor car terms, the engineering is quite simple, but scaling the technology down will present many challenges. Prius consumers were initially nervous about the reliability of the novel electrical components and especially the batteries, but Toyota had sufficient confidence to offer a 100,000-mile warranty on the hybrid drive, which has proved extremely reliable.The same rugged simplicity and fully enclosed transmission would suit a bicycle very well. Moeller is already working with business partners in Taiwan, with the intention of mass producing hub units for just a few hundred dollars, to be fitted to new bicycles or sold as after-market accessories.The future may arrive sooner than you think.
Our grateful thanks to Frank Moeller. For further information, Frank can be contacted at frank.moeller@ntlworld.com
A to B 49 – Aug 2005